Produced MPP Pipes
Raw Material—feeder—single screw extruder—mould and calibrator—vacuum forming machine— spraying cooling machine—haul-off machine—cutting unit— stacker.Processing Process
Vacuum Calibration & Cooling tank The vacuum and cooling unit equip frequency conversion control system for high energy conservation and high space saving. Adequate length of the vacuum and cooling calibration ensure the shaping and cooling of the MPP pipes.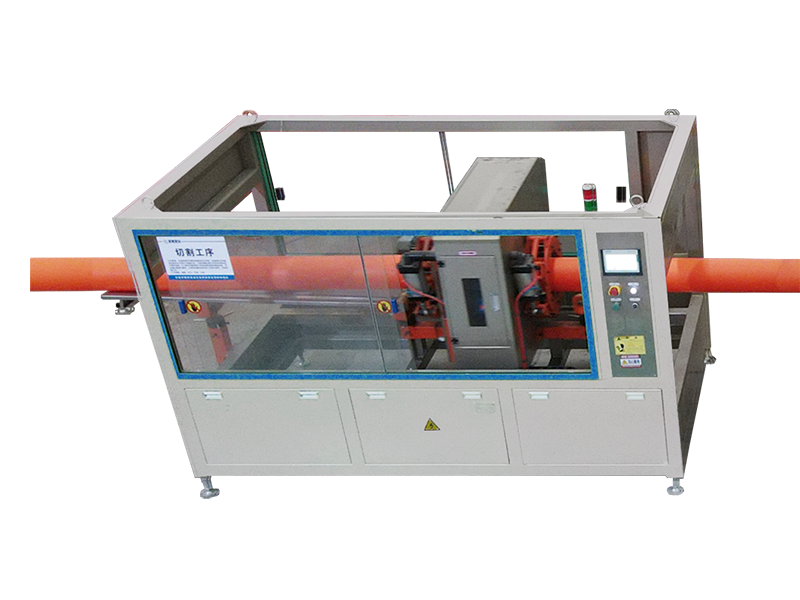
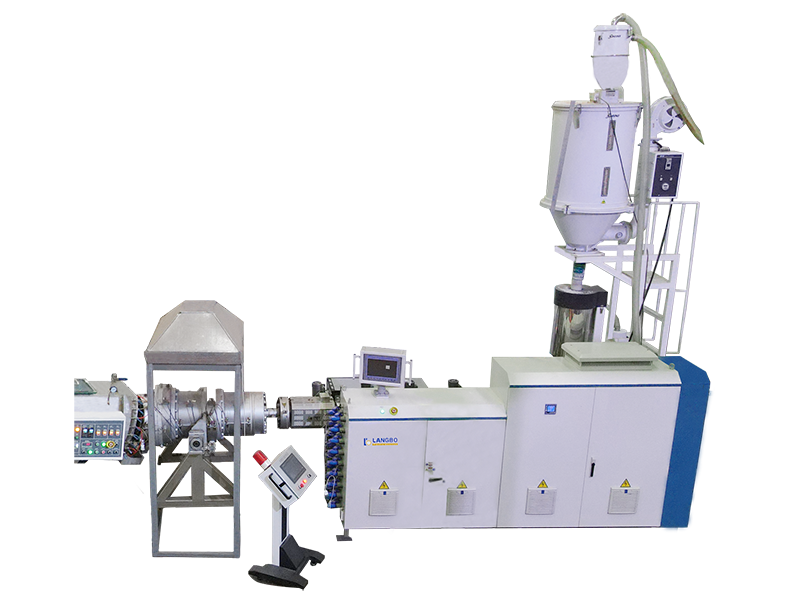
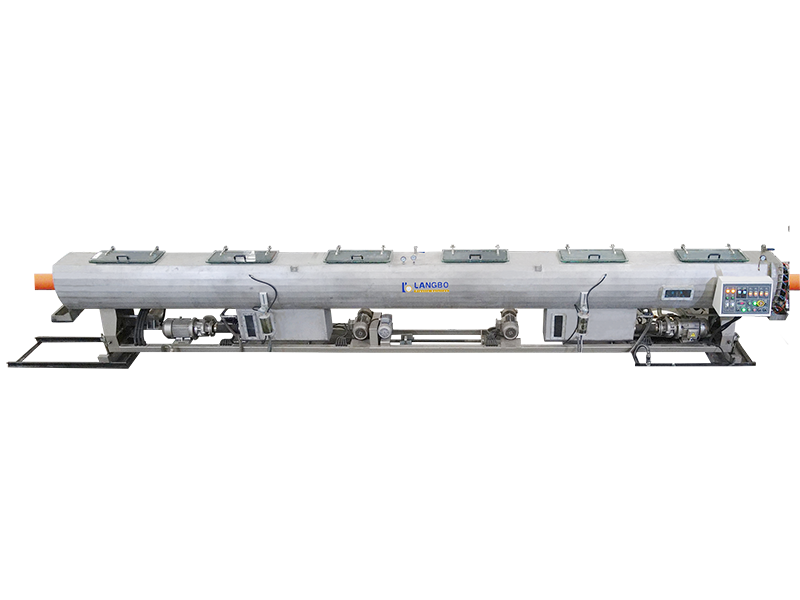
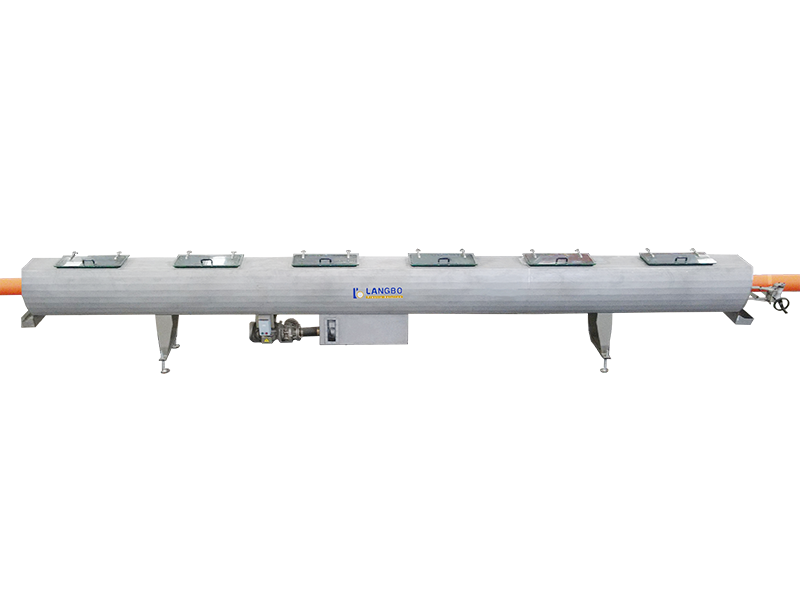
Specifications
Model | Pipe range | Screw Model | Motor power | Total length | Max output |
LB-63 | 16-63mm | SJ65 | 37KW | 22m | 80-120kg |
LB-110 | 20-110mm | SJ75 | 55KW | 30m | 100-160kg |
LB-160 | 50-160mm | SJ75 | 90KW | 35m | 120-250kg |
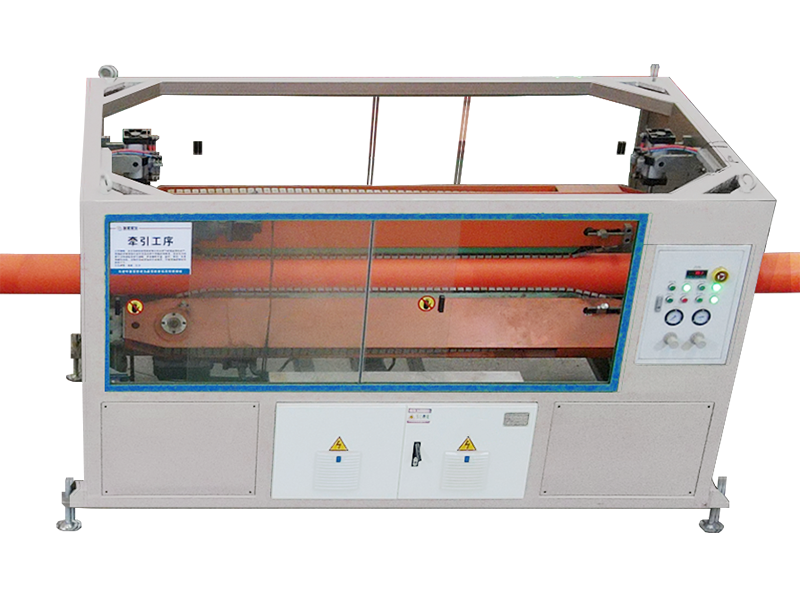
Product detail
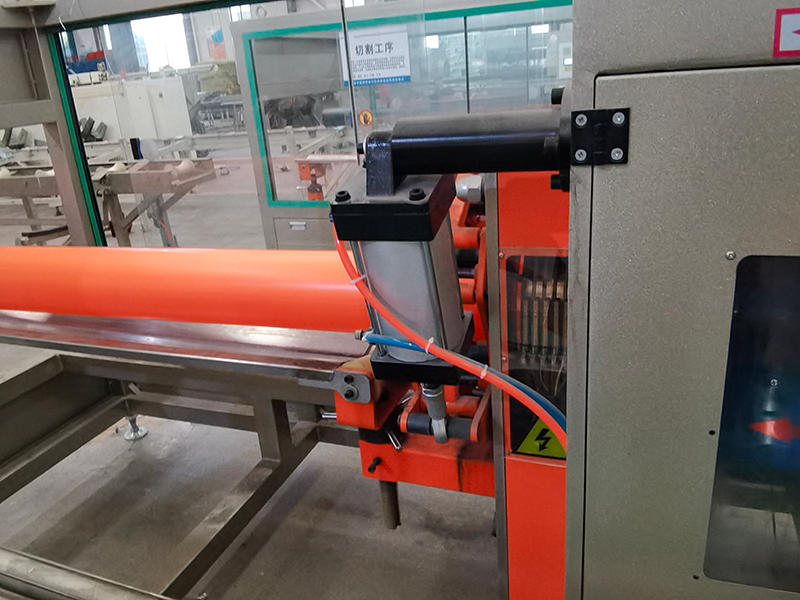
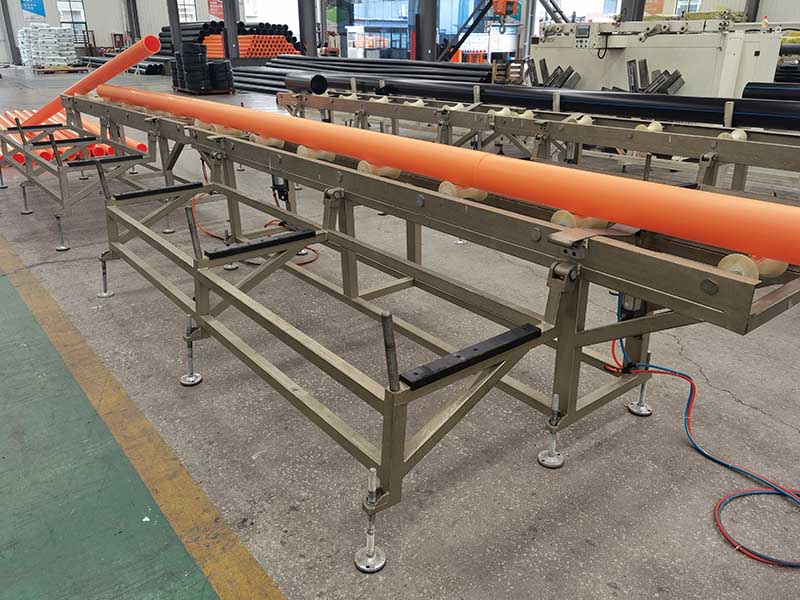
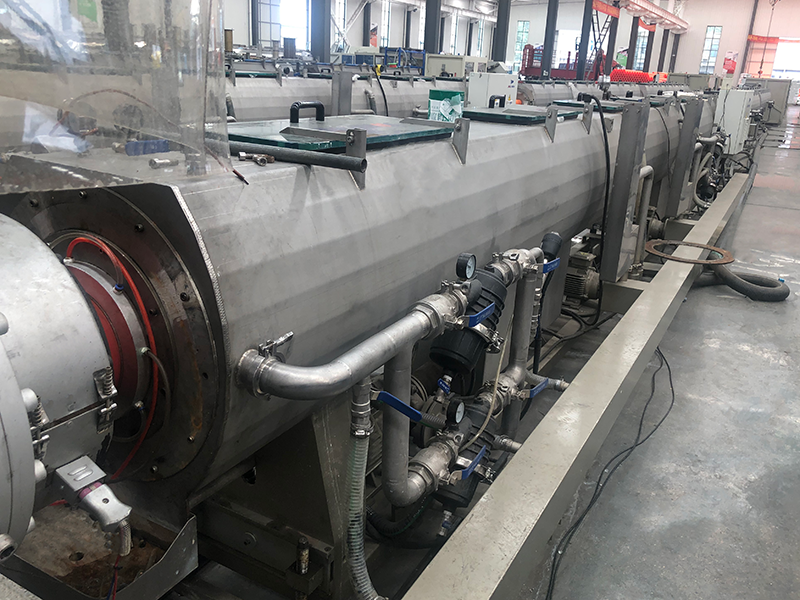
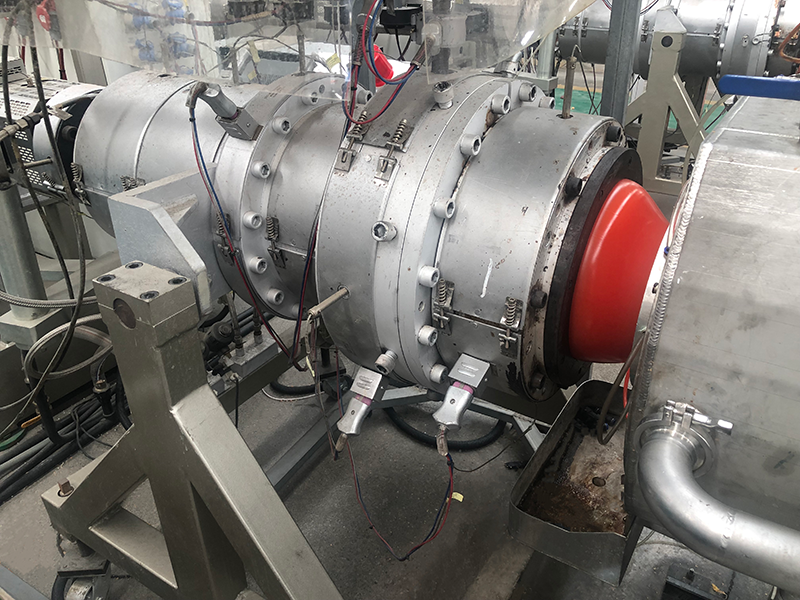
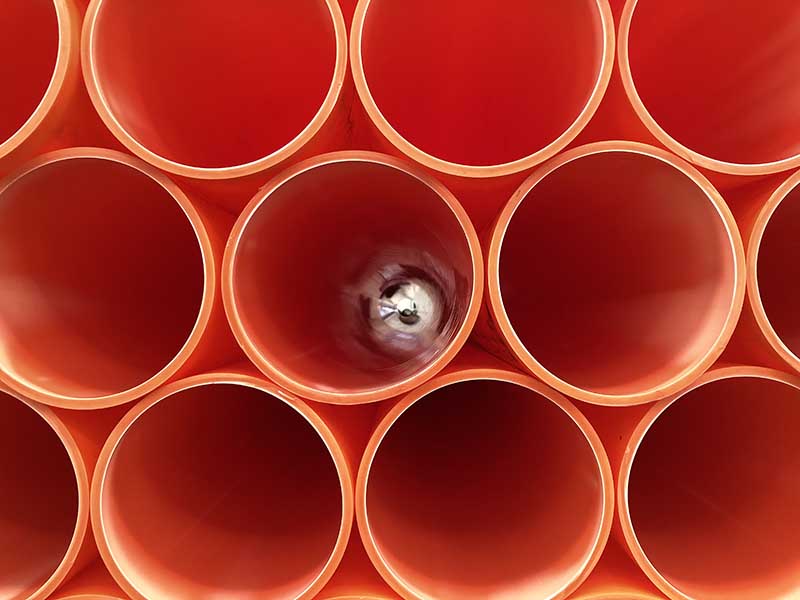
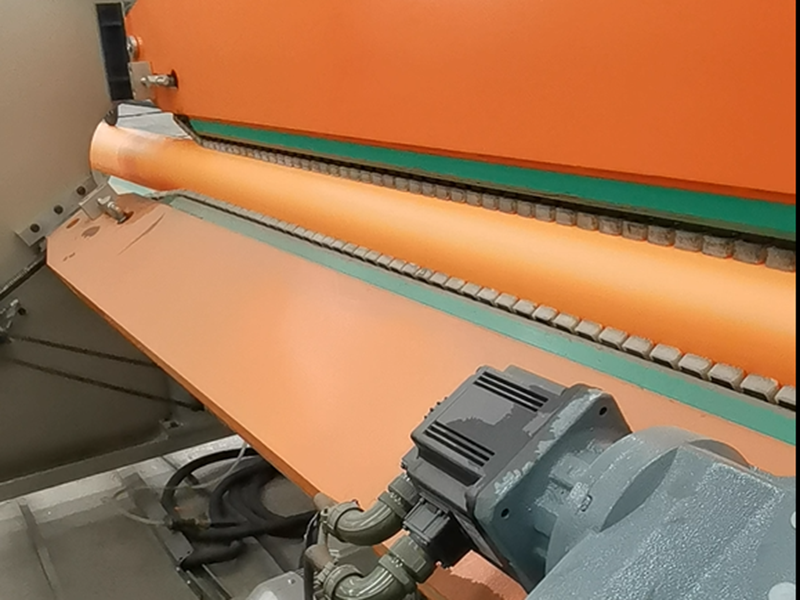
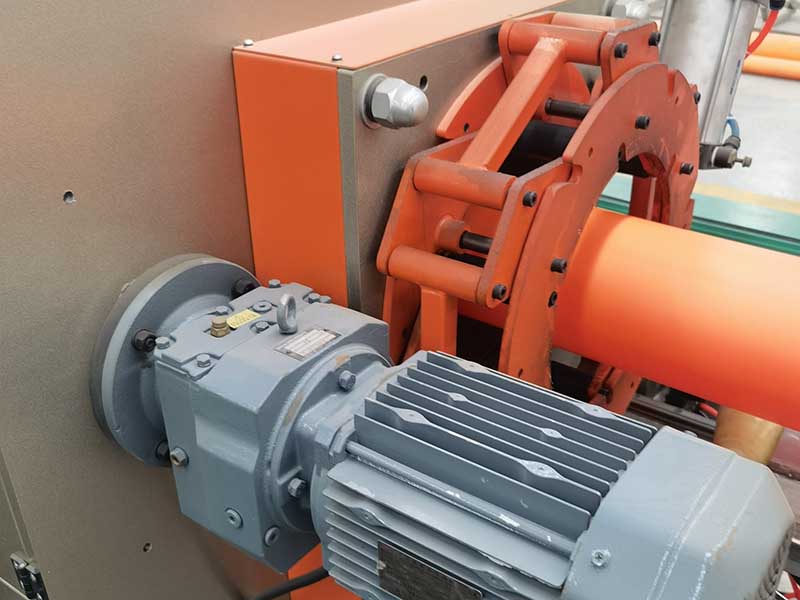
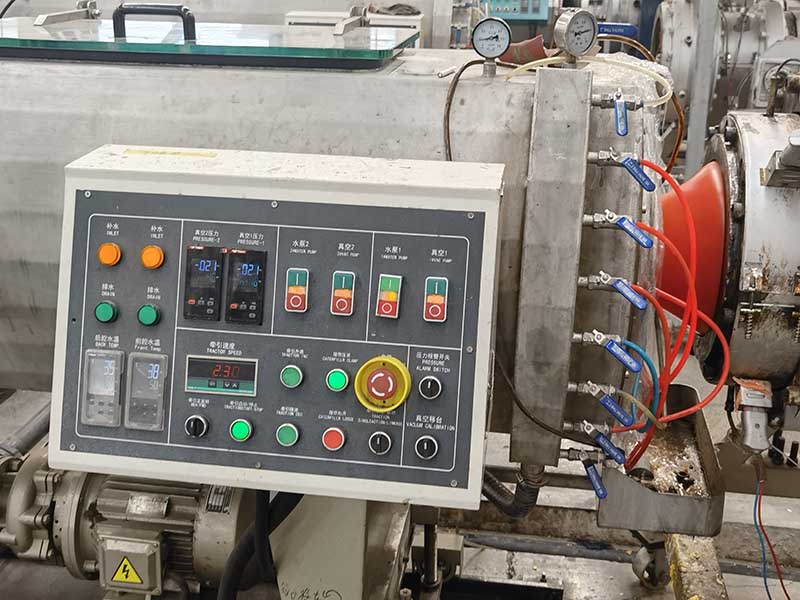
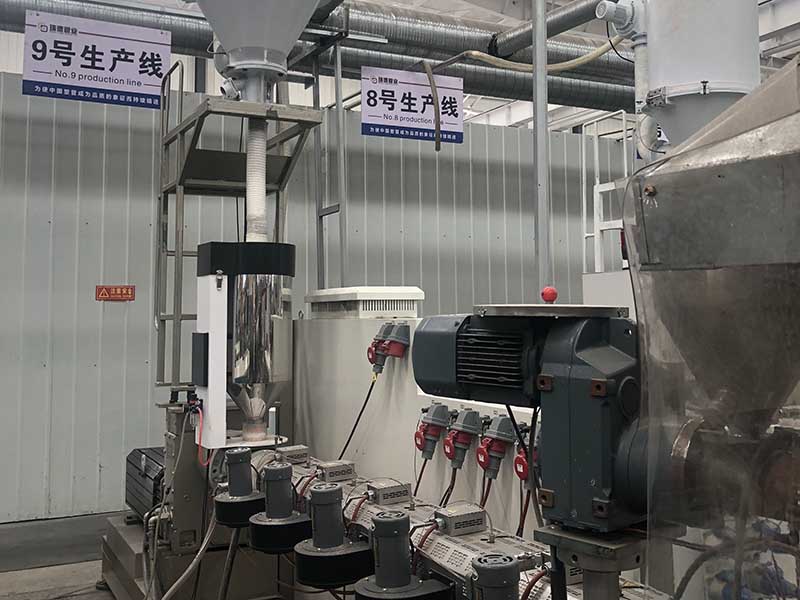
Product Details
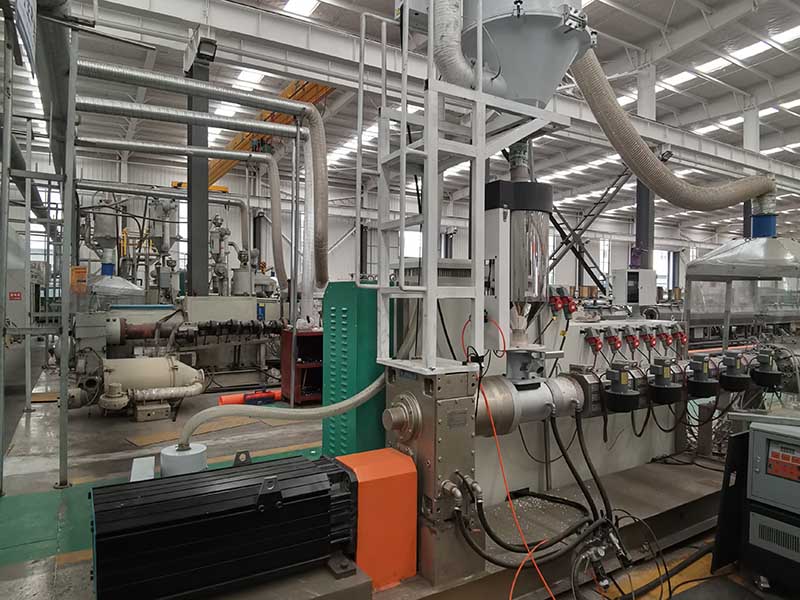
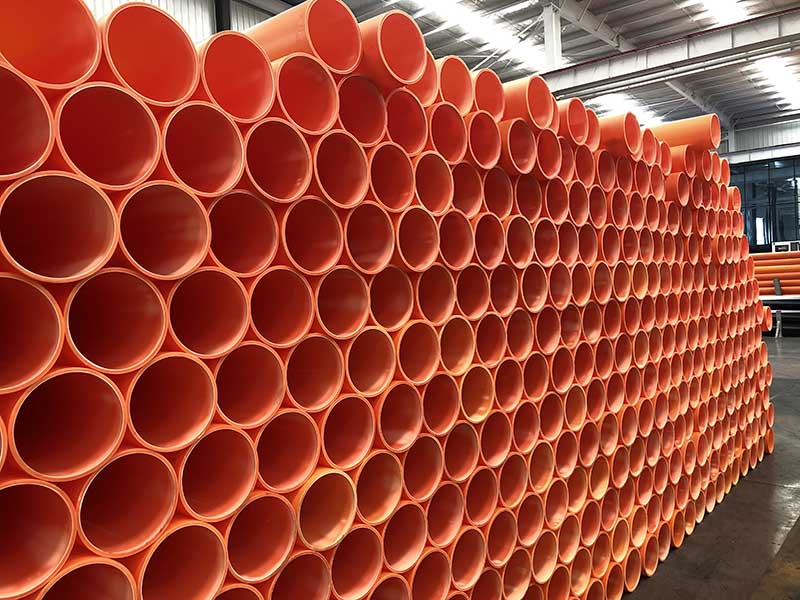